El proceso de control de calidad de la ropa interior masculina no se limita a inspeccionar los productos antes de su comercialización; también es un arte delicado dentro de la industria textil. Para garantizar que cada producto sea no solo estéticamente agradable, sino también seguro para los usuarios, los fabricantes deben implementar este proceso de forma meticulosa y sistemática. Dada su naturaleza delicada y el contacto directo con el cuerpo, la ropa interior masculina requiere un riguroso proceso de inspección para garantizar que el producto cumpla con los estándares de calidad y seguridad.
Además, el proceso de control de calidad refleja la profesionalidad y la responsabilidad del fabricante con la salud del consumidor. En K&G Garment, con más de una década de experiencia y desarrollo en la industria textil, nos comprometemos a ofrecer ropa interior masculina de alta calidad mediante un riguroso proceso de control de calidad. Esto no solo garantiza la satisfacción del cliente, sino que también fortalece la posición de la marca en el competitivo mercado actual.
Estándares de Inspección de Calidad para Ropa Interior Masculina
Para producir ropa interior masculina que cumpla con los estándares, los fabricantes deben adherirse a estrictas regulaciones y normas. La TCVN/QS 1822:2021 es una de las normas más importantes que guía el proceso de control de calidad del producto. Esta norma no solo se centra en la consistencia del producto, sino que también hace hincapié en garantizar la seguridad del usuario.
El proceso de control de calidad se desarrolla en tres etapas: preproducción, inspección durante la producción y postproducción. Cada etapa cuenta con criterios específicos para detectar y eliminar posibles problemas, garantizando así la calidad del producto final. Comprender estos criterios ayudará a los fabricantes a tomar las medidas adecuadas, desde la selección de las materias primas hasta la producción e inspección de los productos terminados.
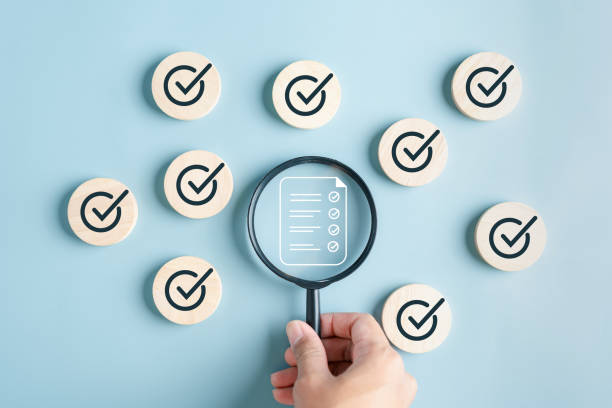
Criterios de Calidad del Producto
La calidad de la ropa interior masculina no solo reside en su apariencia, sino también en la sofisticación de cada detalle. Un producto que cumple con los estándares debe cumplir con los siguientes criterios:
- Inspección Externa: El producto debe cumplir con el estándar de ausencia de defectos superficiales como manchas, exceso de hilos o arrugas. Esta inspección debe realizarse a simple vista inmediatamente después de la fabricación. Esto no solo crea un atractivo estético, sino que también demuestra atención al detalle en cada producto.
- Inspección de Materiales: Los materiales utilizados en la producción deben tener un origen claro y cumplir con los estándares. Las prendas deben ser inspeccionadas para obtener la certificación de calidad, especialmente los componentes que entran en contacto directo con el cuerpo.
- Especificaciones Técnicas: El producto debe cumplir con los requisitos de talla, largo y ancho. Estos deben medirse con una cinta métrica y un calibrador, lo que garantiza que el producto no solo sea atractivo, sino que también se ajuste a las necesidades de los clientes.
Cumplir con estos estándares no solo mejora la reputación del fabricante, sino que también protege los derechos y la salud de los consumidores. A continuación, se presenta una tabla resumen de los criterios de calidad del producto:
Criterios | Descripción |
---|---|
Inspección externa | Acabado superficial sin defectos |
Inspección del material | Los materiales están certificados y tienen un origen claro |
Especificaciones técnicas | El tamaño, el largo y el ancho cumplen con los requisitos |
Cada producto inspeccionado según estos criterios generará una sólida confianza en los clientes y contribuirá a mejorar la calidad de toda la industria textil nacional.
Estándares de seguridad en la producción de ropa interior
La seguridad en la producción de ropa interior masculina es un factor indispensable en el proceso de control de calidad. Los fabricantes deben implementar estrictamente procedimientos de inspección para garantizar que el producto final no solo sea atractivo, sino también seguro para los usuarios.
En primer lugar, las materias primas deben seleccionarse cuidadosamente de proveedores de confianza, garantizando que cumplan con las normas de seguridad e higiene alimentaria (ATVSTP). Estos materiales deben someterse a pruebas para garantizar que no contengan sustancias químicas nocivas, creando un entorno seguro para la salud del consumidor.
A continuación, durante el proceso de producción, todo el procedimiento debe cumplir con las normas internacionales de seguridad ocupacional e higiene alimentaria. No podemos permitir ningún factor que pueda afectar la salud y la seguridad de los consumidores. Esto no es solo responsabilidad de cada empleado, sino también de toda la empresa.
Por último, una vez finalizado el producto, la inspección de calidad final también debe centrarse en los factores de seguridad. Las materias primas y los productos terminados deben inspeccionarse cuidadosamente, desde el material de la tela hasta la durabilidad y la solidez del color después del lavado.
Criterios de seguridad | Descripción |
---|---|
Materiales de entrada | Absolutamente sin productos químicos nocivos |
Proceso de producción | Cumple plenamente con las normas de seguridad e higiene alimentaria |
Inspección final | Garantiza la seguridad sanitaria desde la materia prima hasta el producto terminado |
El énfasis en los estándares de seguridad durante la producción no solo ayudará a proteger la salud del consumidor, sino que también consolidará la reputación de la marca en la industria textil.
Lista de verificación del proceso de producción de ropa interior masculina
Para que el proceso de control de calidad de la ropa interior masculina sea eficaz, es fundamental crear una lista de verificación detallada. Estos criterios ayudarán a garantizar que cada etapa del proceso de producción se lleve a cabo de forma precisa y consistente.
Una lista de verificación no solo ayuda a los fabricantes a gestionar e inspeccionar fácilmente cada paso del proceso, sino que también proporciona una visión general de la calidad del producto. Los pasos de la lista de verificación suelen incluir:
- Comprobación de los materiales de entrada;
- Supervisión del proceso de producción en cada etapa, como corte, costura y procesamiento;
- Inspección de la calidad de los productos terminados antes del almacenamiento.
A continuación, se presenta un ejemplo de lista de verificación para el proceso de producción de ropa interior masculina:
Etapa | Criterios de inspección |
---|---|
Materiales de entrada | Certificado de origen, libre de sustancias químicas nocivas |
Corte de la tela | Precisión de cada pieza de tela |
Costura | Calidad de las puntadas, durabilidad |
Acabado | Verificación de talla, diseño y embalaje |
Una lista de verificación clara ayudará a detectar rápidamente cualquier anomalía y a tomar medidas correctivas oportunas, evitando que productos de baja calidad lleguen a los consumidores.
Pasos en el proceso de producción de ropa interior
El proceso de producción de ropa interior masculina no es solo una serie de actividades, sino también una combinación armoniosa de arte y tecnología. Cada etapa desempeña un papel fundamental para garantizar la calidad final del producto. A continuación, se presentan algunos pasos importantes de este proceso:
- Preparación del material: Materiales como el algodón, el modal y la microfibra deben seleccionarse cuidadosamente de proveedores de confianza, garantizando que cumplan con la norma Oeko-Tex. Se debe verificar la calidad, el tamaño y las características necesarias de los materiales.
- Diseño del producto: Este es un paso crucial para garantizar que el producto no solo sea estéticamente agradable, sino también cómodo para el usuario. El equipo de diseño debe centrarse en crear diseños únicos que, a la vez, sean seguros y prácticos.
- Corte y costura: Los materiales se cortan con precisión con maquinaria moderna, lo que aumenta la precisión. Posteriormente, la costura se realiza con tecnologías avanzadas, lo que garantiza la durabilidad y la estética del producto.
- Control de calidad: Cada producto se somete a un riguroso proceso de control de calidad, que incluye inspección mecánica y manual por parte de personal experimentado. Esto garantiza que cada detalle se cuida al detalle.
- Embalaje: El producto se envasa con materiales ecológicos, lo que ayuda a proteger su calidad durante el transporte.
Paso | Descripción |
---|---|
Preparación del material | Seleccionar materiales que cumplan con los estándares Oeko-Tex |
Diseño del producto | Crear diseños y estilos cómodos |
Corte y costura | Usar tecnología moderna para un corte y una costura precisos |
Control de calidad | Implementar una inspección rigurosa antes de la finalización del producto |
Empaque | Utilizar empaques ecológicos |
Cada paso del proceso de producción refleja cuidado y respeto tanto por el producto como por el cliente. Implementar este proceso correctamente creará productos que no solo sean estéticos, sino también de alta calidad, lo que contribuirá a realzar el valor de la marca.
Lista de verificación de inspección de materiales de entrada
La inspección de los materiales de entrada es un paso fundamental en el proceso de producción de ropa interior masculina, ya que el material es la base que determina la calidad final del producto. Una lista de verificación clara para este paso ayudará a garantizar que los materiales utilizados cumplan con los estándares necesarios.
Una lista de verificación de inspección de materiales de entrada suele incluir los siguientes criterios:
- Origen del material: El material debe tener un origen claro y garantizar que no contenga sustancias químicas nocivas. Esto no solo protege la salud de los consumidores, sino que también contribuye a la protección del medio ambiente.
- Certificación de calidad: Cada tipo de material debe contar con un certificado de seguridad del proveedor. Asegúrese de que cumpla con estándares como Oeko-Tex o ISO 9000.
- Inspección física: Evalúe la calidad del tejido en términos de durabilidad, elasticidad, color y diseño mediante métodos de inspección sensorial.
A continuación se muestra una tabla resumen de la lista de verificación de inspección del material de entrada:
Criterios de inspección | Descripción |
---|---|
Origen del material | Asegurar que los materiales tengan un origen claro |
Certificación de calidad | Verificar los certificados de seguridad e higiene alimentaria del proveedor |
Inspección física | Evaluar la durabilidad, la elasticidad y el color |
Este proceso ayudará a los fabricantes a elegir los mejores materiales para garantizar que la calidad del producto se mantenga durante todo el proceso de producción y llegue a los consumidores.
Lista de verificación de inspección en producción
Durante la producción de ropa interior masculina, la inspección de calidad continua es fundamental. Para garantizar que cada etapa cumpla con los estándares, una lista de verificación detallada ayudará a los empleados a supervisar fácilmente los criterios necesarios.
Una lista de verificación de inspección en producción suele incluir pasos como:
- Comprobación de los materiales antes de la producción: Asegurarse de que todos los materiales hayan sido inspeccionados y cumplan con la calidad de entrada.
- Supervisión de la etapa de corte de la tela: Evaluar minuciosamente las piezas de tela cortadas, asegurándose de que no haya errores y de que cumplan con los requisitos de tamaño.
- Supervisión del proceso de costura: Inspeccionar cada puntada, asegurándose de que sea firme y uniforme.
- Comprobación del procesamiento del producto: Tras la finalización, es necesario inspeccionar el producto para verificar detalles como las etiquetas y el embalaje.
Etapa de producción | Criterios de inspección |
---|---|
Verificación del material de entrada | Asegurarse de que los materiales cumplan con los estándares |
Corte de la tela | Verificar el tamaño y la precisión |
Costura | Calidad y consistencia de la puntada |
Verificación posterior a la producción | Asegurarse de que el producto final no presente defectos |
Estas listas de verificación no solo ayudan a mejorar la eficiencia operativa, sino que también minimizan la tasa de productos defectuosos, manteniendo así la reputación de la marca.

Lista de verificación para la inspección final del producto
Tras completar el proceso de producción, la inspección de calidad final del producto es un paso indispensable. Esta es la última oportunidad para garantizar que el producto cumpla con todos los estándares de calidad antes de su lanzamiento al mercado.
Una lista de verificación para la inspección final del producto suele incluir los siguientes criterios:
- Verificación de tamaño: Medir el tamaño del producto con una cinta métrica o un calibrador para garantizar la precisión de las dimensiones.
- Evaluación externa: Verificar si el producto presenta algún defecto, desde la superficie hasta las costuras.
- Prueba de durabilidad: Realizar pruebas básicas como tracción y estiramiento para garantizar la durabilidad necesaria del producto.
A continuación, se presenta una tabla resumen de la lista de verificación para la inspección final del producto:
Criterios de inspección | Descripción |
---|---|
Verificación de tallas | Asegurarse de que las tallas del producto cumplan con los estándares |
Evaluación externa | Verificar defectos, tacto e inspección visual |
Prueba de durabilidad | Realizar pruebas mecánicas y de elasticidad |
Un proceso de inspección exhaustivo no solo protege la marca, sino que también genera satisfacción en los clientes, contribuyendo a la fidelización y al crecimiento sostenible de la industria textil.
Evaluación de cada etapa de la producción de ropa interior masculina
Para producir ropa interior masculina de alta calidad, es fundamental evaluar cada etapa del proceso de producción. Este proceso no solo garantiza que los pasos se realicen correctamente, sino que también ayuda a identificar las deficiencias que deben abordarse.
Cada etapa, desde la selección del material, el corte, la costura y el acabado, desempeña una función específica. Un registro y una evaluación precisos ayudarán a optimizar el proceso y a crear un producto más completo.
A continuación, se presentan algunos puntos clave para evaluar cada etapa de la producción de ropa interior masculina:
Evaluación del proceso de corte y costura
El proceso de corte y costura son dos pasos importantes en la producción de ropa interior masculina. La evaluación de estas etapas ayuda a garantizar que el producto se fabrique con alta precisión y buena calidad.
- Proceso de corte: Los materiales de tela se cortan con maquinaria moderna, lo que requiere precisión para evitar desperdicios. Es necesario comprobar la calidad de las piezas de tela antes de coserlas.
- Etapa de costura: Este paso determina la durabilidad del producto. El proceso de costura debe aplicar tecnologías modernas, como la costura sin costuras y el uso de máquinas automáticas, para mejorar la firmeza de cada puntada.
- Evaluación general: Es necesario revisar periódicamente todo el proceso, desde el corte hasta la costura, para detectar rápidamente cualquier problema. Los trabajadores deben recibir capacitación constante y mantenerse al día con los nuevos conocimientos para mejorar la calidad del producto.
Criterios | Descripción |
---|---|
Comprobación del corte de la tela | Asegurar el tamaño y la precisión |
Comprobación de la costura | Asegurar que las puntadas sean firmes y consistentes |
Evaluación general | Comprobar y registrar cualquier error que surja |
La inversión y la atención al detalle en las etapas de corte y costura contribuyen significativamente a la calidad del producto final que reciben los clientes.
Evaluación del Proceso de Acabado y Procesamiento
La etapa de acabado y procesamiento juega un papel crucial en la conformación del producto final. Aquí es donde todo el esfuerzo de las etapas anteriores se materializa en un producto completo.
- Comprobación de los pequeños detalles: Es necesario inspeccionar cuidadosamente elementos como las etiquetas de la marca, los botones o los componentes decorativos para evitar daños durante el uso del producto.
- Evaluación de las características del producto: Es necesario revisar minuciosamente la elasticidad, la retención del color después del lavado y la resistencia a las arrugas del producto terminado. Esto no solo crea una buena experiencia para los usuarios, sino que también prolonga la vida útil del producto.
- Garantizar la seguridad: El proceso de acabado debe garantizar que no queden objetos afilados dentro del producto. El uso de tecnología de detección de agujas puede ayudar a identificar objetos no deseados.
Criterios | Descripción |
---|---|
Comprobación de pequeños detalles | Asegurarse de que todos los detalles estén completos |
Evaluación de características | Comprobar la elasticidad, la retención del color y la resistencia a las arrugas |
Garantizar la seguridad | Utilizar tecnología de detección de agujas para encontrar objetos afilados |
Poner énfasis en la etapa de acabado no solo mejora la calidad del producto, sino que también genera confianza en los clientes.
Evaluación del Proceso de Empaquetado y Almacenamiento
El empaquetado y el almacenamiento del producto son los pasos finales del proceso de producción que no pueden pasarse por alto. Evaluar esta etapa puede ayudar a garantizar que el producto llegue a los consumidores en las mejores condiciones posibles.
- Calidad del Empaquetado: El empaquetado no solo protege el producto, sino que también refleja la profesionalidad de la empresa. Un empaquetado cuidadoso causará una buena impresión en los clientes a primera vista.
- Almacenamiento: El proceso de almacenamiento debe realizarse en condiciones óptimas, evitando la humedad y la luz intensa para preservar la calidad a largo plazo. Esto no solo ayuda a que el producto mantenga su calidad, sino que también facilita el proceso de almacenamiento.
- Inspección Final: Antes del almacenamiento, el producto debe revisarse una última vez para garantizar que no haya sufrido daños durante el almacenamiento.
Criterios | Descripción |
---|---|
Calidad del embalaje | Asegúrese de que el producto esté protegido y tenga un aspecto atractivo. |
Almacenamiento | Conservar el producto en buenas condiciones. |
Comprobación final | Asegúrese de que el producto esté siempre en perfectas condiciones. |
Cuidar desde el embalaje hasta la etapa de almacenamiento no solo ayudará a proteger el producto, sino que también construirá una imagen confiable de la marca a los ojos de los clientes.

Métodos para Medir la Calidad del Producto
Medir la calidad del producto es una parte importante del proceso de control de calidad de la ropa interior masculina. El uso de métodos y herramientas adecuados ayudará a los fabricantes a evaluar los productos con precisión y eficacia.
Existen numerosos métodos para medir y controlar la calidad, como la inspección sensorial, la inspección con equipos de medición y el análisis químico. Estos métodos cumplen diferentes propósitos y requisitos en el proceso de producción.
A continuación, se presentan algunos métodos comunes para medir la calidad de la ropa interior masculina:
Métodos de Inspección Sensorial
La inspección sensorial es uno de los métodos más sencillos y comunes para determinar la calidad del producto. Este método se basa en los sentidos humanos, principalmente la vista, el tacto y el olfato, para evaluar las propiedades del producto.
- Inspección del Color y la Superficie: El inspector utilizará la vista para evaluar el color, el brillo y la consistencia del producto. Un producto con una superficie en buen estado y sin defectos causará una buena impresión a primera vista.
- Comprobación de la Suavidad: Utilice las manos para palpar la suavidad de la tela. Esto es muy importante para la ropa interior, ya que afecta a la comodidad del usuario.
- Comprobación del olor: Aunque no se menciona con frecuencia, comprobar el olor también es necesario. Un producto con un olor desagradable o inusual debe retirarse antes de su comercialización.
Criterios | Herramienta de inspección |
---|---|
Color y superficie | Inspección visual |
Suavidad | Tacto |
Olfato | Sentido olfativo |
El método de inspección sensorial sienta las bases para la evaluación inicial, pero debe combinarse con otros métodos para garantizar una mayor precisión.
Inspección con equipo de medición
La inspección con equipo de medición es un método más preciso y científico para evaluar la calidad del producto. El uso de equipo especializado ayudará a evaluar en detalle factores como el tamaño, la durabilidad y la elasticidad.
- Talla: Utilice una cinta métrica y un calibrador para medir la talla del producto, asegurándose de que cumpla con los parámetros técnicos especificados. Esto ayuda a descartar productos que no se ajusten al diseño original.
- Durabilidad: Utilice equipos de prueba de tracción para comprobar la durabilidad del tejido. Esta prueba ayuda a determinar si el producto puede soportar la presión durante su uso.
- Elasticidad: Compruebe la elasticidad con un equipo especial, evaluando la capacidad del tejido para expandirse y recuperar su forma original. Los resultados de esta prueba son muy importantes para garantizar que el producto cumpla con los requisitos de comodidad del usuario.
Criterios | Equipo de medición |
---|---|
Talla | Cinta métrica, calibradores |
Durabilidad | Equipo de ensayo de tracción |
Elasticidad | Equipo de medición de elasticidad |
Los métodos de inspección que utilizan equipos proporcionan una alta precisión y ayudan a minimizar los riesgos en el proceso de producción.

Análisis químico en el control de calidad
El análisis químico desempeña un papel importante en el proceso de control de calidad de la ropa interior masculina. Este método ayuda a verificar la seguridad de los productos químicos utilizados en el proceso de producción, garantizando que el producto no contenga sustancias nocivas antes de su comercialización.
- Comprobación de la composición química: Se utilizan métodos de análisis químico para evaluar la composición del tejido, especialmente productos químicos como tintes y agentes de acabado. Esto ayuda a determinar el nivel de seguridad y el respeto al medio ambiente del producto.
- Evaluación de alergenicidad: Algunos productos químicos pueden causar alergias, por lo que esta comprobación es fundamental. En el caso de la ropa interior, que entra en contacto directo con la piel, es fundamental eliminar los productos químicos potencialmente peligrosos.
- Garantizar los estándares de higiene: El análisis químico ayuda a los fabricantes a garantizar que el producto cumpla con los estándares de higiene y calidad necesarios.
Criterios | Método de inspección |
---|---|
Composición química | Uso de métodos de análisis químico |
Alergenicidad | Realización de pruebas de toxicidad en usuarios |
Estándares de higiene | Evaluación de los niveles de seguridad y cumplimiento de los estándares |
Comparación de métodos de control de calidad para ropa interior masculina
Comparación de la inspección de lotes y la inspección de muestras
Criterios | Inspección de lotes | Inspección de muestras |
---|---|---|
Consistencia | Alta | No garantizada |
Costo | Alta | Bajo |
Tiempo | Consumo de tiempo | Rápido |
Precisión | Muy alta | Posibilidad de errores |
La elección del método de inspección a utilizar depende de las prioridades de cada fabricante y de las características del producto.

Comparación entre la inspección interna y la externa
La inspección interna y la externa son dos tipos de inspección que desempeñan un papel fundamental en la evaluación de la calidad del producto.
- Inspección interna: Este método de inspección es realizado por los empleados de la empresa. Una de sus principales ventajas es que permite detectar errores con antelación y realizar ajustes oportunos durante el proceso de producción. Esto genera flexibilidad y fomenta la creatividad en cada etapa; sin embargo, la desventaja es que puede presentar falta de objetividad y transparencia.
- Inspección externa: Realizada por organizaciones independientes, contribuye a mejorar la fiabilidad de la evaluación de la calidad. Sin embargo, este método suele ser más lento y menos flexible que la inspección interna. Los resultados de la evaluación de una organización independiente también pueden ser difíciles de ajustar con prontitud.
Criterios | Inspección interna | Inspección externa |
---|---|---|
Objetividad | Baja | Alta |
Flexibilidad | Alta | Baja |
Tiempo | Rápido | Completado periódicamente |
Precisión | Dependiendo del empleado | Muy alta |
Cada método tiene sus beneficios y debe utilizarse en paralelo para optimizar el proceso de control de calidad del producto.
Impacto de los procesos de control de calidad en el mercado
El proceso de control de calidad no solo afecta al producto, sino que también tiene un profundo impacto en el mercado. Un proceso de control de calidad profesional y consistente ayudará a mejorar el valor de la marca, generar confianza en los consumidores y aumentar la competitividad en la industria textil.
Cuando un producto se lanza al mercado tras someterse a un riguroso proceso de control de calidad, la fiabilidad y la reputación de la marca aumentan. Esto impulsa las ventas y crea un mayor reconocimiento de marca que nunca.
Impacto en la satisfacción del cliente
La satisfacción del cliente es siempre el objetivo principal de toda empresa. El proceso de control de calidad garantizará que los productos lleguen a los consumidores en las mejores condiciones posibles.
Un producto de calidad no solo cumple con los requisitos de apariencia, sino que también ofrece una alta durabilidad y funcionalidad. Los clientes se sentirán más satisfechos cuando el producto no solo sea atractivo, sino también cómodo de usar. Esto los motivará a volver a la tienda y recomendar el producto a otros.
Nivel de satisfacción | Factores influyentes |
---|---|
Alto | Calidad del producto |
Cómodo | Suavidad y transpirabilidad |
Duradero | Uso duradero |
La satisfacción del cliente no sólo aporta beneficios al negocio sino que también ayuda a construir la marca en la mente de los consumidores.

Impacto en la marca y la reputación empresarial
La marca y la reputación de una empresa están estrechamente vinculadas al proceso de control de calidad. Un control de calidad profesional no solo ayuda a que el producto cumpla con los estándares, sino que también reafirma el compromiso de la empresa con los clientes.
Cuando un producto es de buena calidad, los clientes aprecian la marca y confían en ella. Esto crea una comunidad de consumidores fieles, dispuestos a volver a comprar productos de esa marca en el futuro.
Factor | Impacto en la marca |
---|---|
Calidad del producto | Mejora la reputación de la marca |
Confiabilidad | Genera confianza en los clientes |
Retroalimentación positiva | Crea oportunidades de expansión del mercado |
El impacto del proceso de control de calidad no se limita a garantizar la seguridad del producto, sino que también contribuye a construir una marca sostenible en el corazón de los clientes.
Conclusiones clave
- El proceso de control de calidad de la ropa interior masculina implica muchos pasos importantes, desde la inspección de las materias primas hasta el producto final.
- La atención a cada etapa no solo mejora la calidad del producto, sino que también protege la salud del consumidor.
- Los diferentes métodos de inspección, incluyendo las inspecciones de lote, de muestra, internas y externas, presentan similitudes y diferencias que deben considerarse.
Conclusión
El proceso de control de calidad de la ropa interior masculina es una parte indispensable de la industria textil moderna. Para crear productos que no solo sean estéticos, sino también de alta calidad, los fabricantes deben dominar y aplicar estándares estrictos en cada etapa de la producción. La visibilidad de la marca y la fidelización del cliente son los logros que un buen proceso de control de calidad puede aportar. De esta manera, podemos ver que la calidad del producto no solo es un factor competitivo, sino también una misión que todo fabricante debe perseguir.