La Manufactura Esbelta (Lean Manufacturing) es una filosofía de producción diseñada para optimizar el valor para los clientes mediante la eliminación de desperdicios. Desarrollada a partir del Sistema de Producción Toyota (TPS), la Manufactura Esbelta (Lean Manufacturing) no es simplemente un conjunto de reglas o procesos, sino un enfoque integral que ayuda a las organizaciones a lograr una producción más eficiente, flexible y sostenible. En el competitivo entorno actual, aplicar la Manufactura Esbelta se ha convertido en un requisito indispensable para que las empresas satisfagan las crecientes demandas del mercado.
La Manufactura Esbelta no solo ayuda a aumentar la productividad, sino que también permite a las empresas gestionar mejor los recursos, desde los humanos hasta las materias primas. Como resultado, las empresas no solo ahorran costos, sino que también mejoran la calidad del producto y la satisfacción del cliente. Este artículo profundizará en los principios fundamentales de la Manufactura Esbelta y en las herramientas y estrategias específicas para implementar eficazmente este método de producción en las empresas.
Principios Fundamentales de la Manufactura Esbelta
La Manufactura Esbelta se basa en cinco principios fundamentales, cada uno de los cuales aporta valor práctico para mejorar los procesos de producción. Estos principios incluyen:
- Identificar el Valor: Comprender claramente el valor que los clientes esperan de un producto o servicio.
- Mapear el Flujo de Valor: Analizar los pasos del proceso de producción para identificar las actividades que generan desperdicios.
- Crear Flujo: Garantizar que el proceso de producción se desarrolle de forma continua e ininterrumpida.
- Establecer Pull: Producir únicamente cuando haya un pedido del cliente, lo que ayuda a minimizar el inventario.
- Buscar la Perfección: Mejorar continuamente para optimizar la calidad y la eficiencia.
Este enfoque no se limita a la mejora de procesos, sino que también puede considerarse un cambio de mentalidad dentro de la organización. Por lo tanto, el consenso y el compromiso de todos los miembros de la empresa son cruciales para garantizar que la aplicación de Lean logre los resultados deseados.

Enfoque en el Valor
Una de las características destacadas de la Manufactura Esbelta es su enfoque en identificar el valor desde la perspectiva del cliente. Para ello, las empresas necesitan estrategias específicas para escuchar las opiniones y necesidades de los clientes. Esto se realiza mediante diversas formas, como encuestas, entrevistas y análisis del comportamiento del cliente.
Comprender claramente el valor no solo ayuda a las empresas a producir productos que cumplan con los requisitos, sino que también genera la máxima rentabilidad durante el proceso comercial. En el entorno competitivo actual, es fundamental comprender rápidamente las tendencias de consumo. Si las empresas producen productos inadecuados o innecesarios, sin duda se desperdiciará tiempo y recursos.
Además de identificar el valor, las empresas también necesitan optimizar el proceso de producción para aumentar el valor del producto. Esto se puede lograr mediante la aplicación de herramientas Lean como las 5S y los Indicadores Clave de Rendimiento (KPI). A continuación, se presenta una lista de algunos factores que ayudan a aumentar el valor:
- Mejorar la Calidad del Producto: Mediante la mejora de los procesos de producción y la aplicación de tecnología avanzada.
- Mejorar la Satisfacción del Cliente: Proporcionando productos que cumplan con los estándares y se entreguen a tiempo.
- Minimizar riesgos: financieros y de tiempo mediante una gestión eficaz de la cadena de suministro.
Al centrarse en el valor, las empresas pueden optimizar sus beneficios y crear un proceso de producción más eficiente, fortaleciendo así continuamente su competitividad.
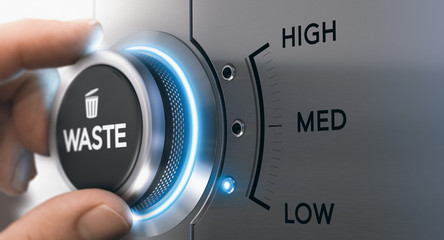
Eliminación de Desperdicios: Los 7 Desperdicios en Lean Manufacturing
Para implementar la Manufactura Esbelta de forma eficaz, identificar y eliminar los desperdicios es fundamental. Existen siete tipos de desperdicios en la Manufactura Esbelta:
- Sobreproducción: Se produce cuando una empresa produce más de lo que demanda, lo que genera grandes inventarios y altos costos de gestión.
- Inventario: El almacenamiento excesivo de materias primas o productos afecta el flujo de caja.
- Movimiento: Los movimientos innecesarios de trabajadores pueden reducir la eficiencia laboral.
- Transporte: Mover materiales entre etapas sin generar valor real.
- Espera: El tiempo en que los empleados o el equipo están inactivos reduce la productividad.
- Defecto: Productos que no cumplen con los estándares requeridos, lo que genera costos adicionales y tiempo de producción.
- Sobreprocesamiento: Utilizar más pasos de los necesarios sin agregar valor al producto.
La eliminación de desperdicios es un proceso continuo que requiere que las empresas cuenten con estrategias y estándares claros para controlar las actividades del proceso de producción. Muchas empresas han aplicado técnicas como el Análisis de Tiempo y el Mapeo del Flujo de Valor para identificar desperdicios en sus procesos.
Los beneficios de eliminar el desperdicio no se limitan al ahorro de costos, sino que también contribuyen a crear un ambiente de trabajo más positivo. A partir de ahí, el personal podrá concentrarse en sus tareas principales, lo que contribuye a la productividad y la calidad del producto.
Mejora Continua de Procesos
La mejora continua de procesos es uno de los principios fundamentales de la Manufactura Esbelta (Lean Manufacturing). Este principio no solo ayuda a las empresas a optimizar los procesos de producción, sino que también fomenta la participación de todos los empleados. Al aplicar el principio Kaizen, las empresas pueden resolver problemas y construir una cultura de mejora.
En la práctica, Kaizen no se trata simplemente de corregir errores o deficiencias en la producción. También implica fomentar la creatividad y las ideas de todos los miembros de la organización. Los empleados se sentirán más comprometidos y responsables al participar aportando ideas para la mejora. Las actividades de mejora de procesos pueden incluir:
- Organizar reuniones de equipo para discutir problemas y soluciones de mejora.
- Proponer medidas para optimizar los procesos de producción.
- Analizar y supervisar la eficacia de cada medida de mejora.
La mejora de procesos no solo beneficia a la empresa, sino que también ayuda a los empleados a desarrollar habilidades y aumentar la satisfacción laboral. La participación de todos en el proceso de mejora continua contribuye a construir una mejor cultura de producción, mejorando así la eficiencia laboral.
Método de Implementación de la Manufactura Esbelta
Para implementar la Manufactura Esbelta de forma eficaz, es fundamental llevar a cabo cada paso de forma organizada y lógica. Al iniciar este proceso, las empresas necesitan un plan claro para los objetivos y métodos de aplicación de los principios Lean. Los pasos de implementación pueden incluir:
- Definir objetivos: Las empresas deben tener objetivos claros para la implementación Lean, de modo que el personal comprenda los objetivos a alcanzar.
- Evaluar el estado actual: Realizar un análisis exhaustivo del proceso de producción actual, identificar desperdicios y oportunidades de mejora mediante el mapeo del flujo de valor.
- Crear un equipo Lean: Elegir un equipo de liderazgo de diferentes departamentos para liderar el proceso de implementación Lean.
- Capacitar a los empleados: Proporcionar conocimientos y habilidades relacionadas con las herramientas Lean a los empleados.
- Aplicar herramientas Lean: Utilizar herramientas como las 5S, Kanban y Justo a Tiempo para optimizar los procesos.
Una vez identificados los principios y métodos básicos, es necesario mantener y mejorar continuamente el proceso de producción para satisfacer rápidamente las necesidades del cliente. El compromiso de la dirección y de todos los departamentos es fundamental para una implementación fluida y eficaz de la Manufactura Lean.
Herramientas Lean Populares
Durante la implementación de la Manufactura Esbelta, es fundamental contar con herramientas de apoyo que ayudan a optimizar el proceso. A continuación, se presentan algunas herramientas Lean populares:
- 5S: Este método optimiza el espacio de trabajo eliminando elementos innecesarios y reorganizando todos los elementos dentro del espacio disponible.
- Ordenar (Seiri)
- Ordenar (Seiton)
- Brillante (Seiso)
- Estandarizar (Seiketsu)
- Sostener (Shitsuke)
- Kaizen: Enfatiza la mejora continua en todos los aspectos del proceso de producción. Los trabajadores de diferentes niveles pueden aportar ideas y participar en la mejora.
- Kanban: Un sistema de gestión de la producción que ayuda a ajustar las actividades de producción según la demanda del cliente, evitando así el inventario.
- Justo a Tiempo (JIT): Un método de producción basado en el tiempo exacto requerido por el cliente, que ayuda a minimizar el inventario.
Estas herramientas no solo ayudan a las empresas a mejorar los procesos, sino que también aumentan la satisfacción del cliente mediante productos de alta calidad y entregas rápidas. Además, la aplicación de herramientas Lean también genera flexibilidad en la producción, satisfaciendo mejor las demandas repentinas del mercado.
El rol del liderazgo en la aplicación de Lean Manufacturing
El rol del liderazgo es uno de los factores decisivos para el éxito de la aplicación de Lean Manufacturing. No solo como director, los líderes deben convertirse en inspiración y modelos a seguir para todos los empleados de la organización.
Un líder exitoso en la aplicación de Lean Manufacturing es alguien que motiva y anima constantemente al personal. Debe crear un ambiente abierto donde se escuchen e implementen las ideas e iniciativas de todos los niveles.
El liderazgo también desempeña un papel importante en la construcción de una cultura Lean dentro de la empresa. Esto incluye la capacitación de los empleados, su motivación para participar en el proceso de mejora y la valoración de sus contribuciones. Por ejemplo, algunas empresas pueden celebrar ceremonias mensuales de recompensa para los empleados que aportan ideas para mejorar los procesos de producción.
Para que los líderes moldeen y mantengan el espíritu Lean en la organización, deben comunicarse regularmente, proporcionar información y actualizar el progreso de los proyectos Lean. Solo así todo el equipo de la empresa podrá trabajar en conjunto hacia un objetivo común, donde todos participen activamente en el proceso de mejora.
Directrices para el Desarrollo de una Cultura Lean en la Organización
Desarrollar una cultura Lean en la organización requiere un fuerte compromiso por parte de la dirección, así como la participación activa de los empleados. Para construir una cultura Lean sostenible, se deben seguir los siguientes pasos:
- Capacitación y Formación: Organizar cursos Lean para empleados de todos los niveles, desde los más bajos hasta los más altos, para que comprendan claramente el valor y los efectos de este método. Esta comprensión motivará a todos a participar en el proceso de mejora.
- Crear un Espacio de Intercambio: Establecer canales de comunicación para que los empleados puedan compartir ideas y comentarios sobre los procesos actuales.
- Fomentar la Participación: Animar a los empleados a participar en proyectos de mejora y a buscar constantemente nuevas soluciones a los problemas. Esto no solo contribuye a mejorar los procesos, sino que también eleva la moral de los empleados.
- Criterios de Evaluación: Establecer indicadores para medir la eficacia de las actividades de mejora de procesos. Esto ayuda a generar una presión positiva para que los empleados mejoren la calidad de su trabajo.
Desarrollar una cultura Lean en la organización no es solo un beneficio a corto plazo, sino también un recurso necesario para el desarrollo a largo plazo del negocio. Cuando se ha establecido una cultura Lean, la empresa puede adaptarse fácilmente y estar preparada para afrontar los cambios en el entorno empresarial.

Comparación de la Manufactura Esbelta con Otros Métodos de Producción
La Manufactura Esbelta y otros métodos de producción, como Six Sigma, Kanban o la Gestión Tradicional, tienen sus propias características para satisfacer las necesidades de las empresas. Mientras que Lean se centra principalmente en la eliminación de desperdicios y la optimización de procesos, Six Sigma enfatiza la reducción de errores mediante el uso de datos y herramientas estadísticas.
La Manufactura Esbelta suele aplicar un método de mejora continua, mientras que Six Sigma se basa en pasos precisos como DMAIC (Definir, Medir, Analizar, Mejorar, Controlar) para lograr los mejores resultados. Kanban, una herramienta de Lean, ayuda a gestionar los procesos y el volumen de producción con mayor flexibilidad, mientras que la gestión tradicional se centra en la previsión de la demanda y la producción a gran escala.
Manufactura Esbelta vs. Six Sigma
Tanto la Manufactura Esbelta como Six Sigma son métodos destacados de gestión de la producción, pero tienen objetivos y enfoques diferentes. Lean se centra en la mejora de los procesos y la eliminación de desperdicios, con el objetivo de maximizar el valor para los clientes mediante la optimización de los procesos de producción. Por otro lado, Six Sigma enfatiza la minimización de errores y defectos mediante el análisis de datos y las estadísticas.
Una clara diferencia entre Lean y Six Sigma reside en su enfoque. Lean suele priorizar la flexibilidad y la velocidad de producción, lo que permite a las empresas responder con rapidez a las necesidades cambiantes de los clientes. Por el contrario, Six Sigma es más técnico y cuenta con un proceso más estructurado. Para una comparación más clara, se presenta la siguiente tabla:
Criterios | Manufactura esbelta | Seis Sigma |
---|---|---|
Enfocar | Eliminando desperdicios | Minimizar errores |
Acercarse | Mejora rápida | Metodología Estructurada |
Objetivo final | Maximizar el valor del cliente | Garantizar la calidad |
Cuando estos dos métodos se combinan, pueden aportar beneficios superiores al negocio, creando condiciones para el desarrollo sostenible y la mejora continua de los procesos de producción.

Manufactura Esbelta vs. Gestión Tradicional
Al comparar la Manufactura Esbelta con la gestión tradicional, la diferencia radica en cómo se planifican y se ejecutan las acciones. En el modelo tradicional, las empresas suelen automatizar procesos basándose en pronósticos y planificación previa. Esto puede generar un exceso de materias primas o productos, lo que genera déficits financieros e ineficiencia productiva.
En cambio, la Manufactura Esbelta ofrece un enfoque completamente diferente. La Manufactura Esbelta fomenta la producción y el suministro de productos en función de la demanda real de los clientes, lo que no solo ayuda a reducir el inventario, sino que también optimiza el proceso de producción. Algunas diferencias clave entre la Manufactura Esbelta y la gestión tradicional incluyen:
- Calidad: La Manufactura Esbelta se centra en la mejora continua de la calidad desde el origen del producto, mientras que la gestión tradicional suele verificar la calidad después de la producción.
- Velocidad: La Manufactura Esbelta enfatiza la mejora de procesos para acortar el tiempo de producción, mientras que la gestión tradicional puede retrasarse debido a la gestión de pasos complejos.
Se puede entender que la Manufactura Esbelta no es solo un método, sino también una filosofía cuyo objetivo es crear el máximo valor para los clientes y eliminar el desperdicio.
Beneficios y limitaciones de la Manufactura Esbelta
La Manufactura Esbelta ofrece numerosos beneficios a las empresas, pero también presenta algunas limitaciones. En primer lugar, el mayor beneficio de la Manufactura Esbelta es la reducción de los costos de producción al eliminar el desperdicio. No solo se reduce la cantidad de inventario, sino que también ayuda a las empresas a ahorrar tiempo en el proceso de producción.
Además, la Manufactura Esbelta ayuda a mejorar la calidad del producto, lo que aumenta la satisfacción del cliente. Las empresas pueden mantener un nivel de calidad estable gracias a la profunda participación de los empleados en el proceso de control de calidad.
Sin embargo, la Manufactura Esbelta también presenta ciertas limitaciones. Implementar la Manufactura Esbelta puede ser difícil si no existe el compromiso de la alta dirección o si los empleados no están acostumbrados a una mentalidad de mejora continua.
Además, la Manufactura Esbelta puede provocar escasez de inventario en caso de un aumento repentino de la demanda. En particular, la sensación de presión derivada de la mejora continua puede incomodar a algunos empleados.
A continuación, se presenta una tabla resumen de los beneficios y limitaciones de la Manufactura Esbelta:
Beneficios | Limitaciones |
---|---|
Reducir los costos de producción | Requiere un fuerte compromiso del liderazgo |
Mejorar la calidad del producto | Difícil de hacer la transición |
Mejorar la satisfacción del cliente | Pueden producirse escasez de inventario |
Lean Manufacturing ofrece una perspectiva diferente y avanzada sobre la producción moderna, ayudando a las empresas a mantener la competitividad y desarrollarse de forma sostenible en un entorno empresarial que cambia rápidamente.

Resultados reales al aplicar la Manufactura Esbelta
Al observar los resultados reales de la Manufactura Esbelta, se observa que no se trata de una teoría descabellada, sino que aporta claros beneficios a las empresas. Un ejemplo típico es Toyota, un fabricante de automóviles de renombre mundial. Al aplicar los principios Lean en su sistema de producción, Toyota ha optimizado con éxito procesos, reducido costos de producción y aumentado la velocidad de respuesta a las demandas del mercado.
Muchas empresas que actualmente aplican Lean también han obtenido resultados positivos. Por ejemplo, algunas empresas reportan aumentos de productividad de hasta un 20% y una reducción del 45% en costos laborales en un corto período. El tiempo del ciclo de producción también se ha reducido de 16 semanas a aproximadamente 5-6 días.
Esto confirma que la Manufactura Esbelta no es solo una tendencia temporal, sino un método sólido que ayuda a las empresas modernas a optimizar procesos y fortalecer su posición competitiva en el mercado.
Mejora de la Eficiencia Productiva
La Manufactura Esbelta tiene como objetivo principal mejorar la eficiencia productiva y, de hecho, muchas empresas lo han logrado aplicando los principios Lean a sus operaciones. Cuando empleados y líderes trabajan juntos para implementar mejoras, la eficiencia laboral mejora significativamente. Las mejoras se promueven considerablemente eliminando actividades innecesarias y optimizando los procesos paso a paso. Por ejemplo, en una planta de fabricación, la reorganización de productos y materiales para mayor comodidad ayuda a eliminar costos innecesarios derivados del transporte y las operaciones redundantes.
Los indicadores de rendimiento también se convierten en herramientas que ayudan a las empresas a realizar un seguimiento diario del proceso de mejora. Podemos observar los cambios en la siguiente tabla:
Indicador | Antes de aplicar Lean | Después de aplicar Lean |
---|---|---|
Tiempo de finalización | 16 semanas | 5 semanas |
Costo de producción | 100 millones | 55 millones |
Productividad laboral | 100 unidades/día | 125 unidades/día |
El aumento de la eficiencia no se limita a la producción, sino que también se refleja en la calidad del servicio al cliente. A medida que los procesos se simplifican y organizan, también aumenta la capacidad de atender las necesidades de los clientes, generando así un gran valor tanto para la organización como para los clientes.

Reducción de Costos y Tiempo de Mano de Obra
Lo primero que aporta la Manufactura Esbelta es una clara reducción en los costos de producción. Al eliminar actividades innecesarias, las empresas pueden ahorrar significativamente en costos de mano de obra. Por ejemplo, en estudios recientes, se han registrado reducciones de costos de mano de obra de hasta un 45% en poco tiempo tras aplicar la Manufactura Esbelta.
Además de reducir los costos de mano de obra, la Manufactura Esbelta también ayuda a acortar el tiempo de producción. Al optimizar y eliminar pasos innecesarios del proceso, también se reduce el tiempo de producción de cada producto. Esta mejora ayuda a aumentar la capacidad de suministro y a mejorar la satisfacción del cliente.
Para ilustrar este impacto con mayor claridad, presentamos la siguiente tabla comparativa:
Criterios | Antes de aplicar Lean | Después de aplicar Lean |
---|---|---|
Costo de mano de obra | 100 millones | 55 millones |
Tiempo de producción | 16 semanas | 5 semanas |
El tiempo de entrega | 4-20 semanas | 1-4 semanas |
Los resultados muestran que la aplicación de Lean Manufacturing no solo ayuda a ahorrar costes, sino que también crea un proceso de producción rápido y flexible, satisfaciendo mejor las demandas del mercado.
Mejora de la calidad del producto
La alta calidad de los productos es siempre el objetivo final de la Manufactura Lean. Mediante la mejora de los procesos, Lean Manufacturing no solo ayuda a reducir el desperdicio, sino que también contribuye a mejorar la calidad del producto. La mejora continua ayuda a las empresas a controlar mejor cada paso del proceso de producción, minimizando así errores y defectos.
Al aplicar Lean Manufacturing, los estándares de calidad se convierten en una parte importante del entorno laboral. Los empleados recibirán formación periódica para comprender claramente los procesos de trabajo y sus responsabilidades en el mantenimiento de la calidad del producto. Esto no solo ayuda a minimizar los errores, sino que también genera confianza en los clientes.
Un producto de buena calidad no solo se basa en el proceso de producción, sino también en la gestión de la calidad. Centrarse en la mejora de la base del producto ayuda a las empresas a crear productos cada vez más perfectos. A continuación, se muestra una tabla comparativa de la calidad del producto antes y después de aplicar Lean Manufacturing:
Criterios | Antes de aplicar Lean | Después de aplicar Lean |
---|---|---|
Tasa de defectos | 10% | 1% |
Nivel de satisfacción del cliente | 70% | 95% |
De los datos anteriores se desprende que la mejora de la calidad del producto es un beneficio innegable de la Manufactura Esbelta. Esto no solo contribuye a mejorar la imagen de marca, sino que también fomenta la fidelización del cliente.

Industrias que aplican con éxito la Manufactura Esbelta
La Manufactura Esbelta ha demostrado su gran aplicabilidad en diversas industrias. Los resultados reales de la aplicación de la Manufactura Esbelta no se limitan a un solo sector, sino que se extienden a diversos campos, como la fabricación de automóviles y la producción de ropa interior masculina.
Manufactura Esbelta en la Fabricación de Automóviles
La industria automotriz es una de las pioneras en la aplicación de la Manufactura Esbelta. Toyota, empresa pionera en el desarrollo de la Manufactura Esbelta, ha logrado crear un proceso de producción eficiente, flexible y sostenible.
El Sistema de Producción Toyota (TPS) se ha convertido en un modelo para muchas empresas de la industria automotriz. Al aplicar la Manufactura Esbelta, Toyota no solo ha minimizado los costos de producción, sino que también ha aumentado la velocidad de respuesta a las demandas del mercado.
Los resultados de la aplicación de la Manufactura Esbelta en Toyota han demostrado:
- Incremento de la productividad laboral del 25 % al 30 %.
- Reducción del tiempo de producción del 30 % al 15 %.
Gracias a estas mejoras, Toyota ha consolidado una marca sólida y mantenido su posición dominante en el mercado automotriz global. Cada producto que lanza no solo ofrece una excelente calidad, sino que también satisface plenamente las necesidades del cliente.
Lean en la producción de ropa interior masculina
La industria de fabricación de ropa interior masculina también se encuentra en plena adopción de la Manufactura Esbelta. Empresas como Tien Bo Garment Group y Garmex Saigon Co., Ltd. han implementado la Manufactura Esbelta y han demostrado éxito en la optimización de sus procesos de producción.
Al aplicar los principios Lean, las empresas han reducido el tiempo de cambio de códigos de producto de 8 a 4 horas, logrando un aumento del 30% en la productividad laboral. Al mismo tiempo, la optimización del proceso de producción no solo contribuye a aumentar la productividad, sino que también mejora el control de la calidad del producto.
Gracias a la aplicación de Lean, estas empresas han mejorado su capacidad de respuesta rápida al mercado y crear productos de mayor calidad para los clientes. Estos notables resultados demuestran que la Manufactura Esbelta es un factor clave para el éxito en todos los sectores manufactureros.
Retos en el proceso de aplicación de la Manufactura Esbelta
Si bien la Manufactura Esbelta promete numerosos beneficios para las empresas, su implementación también enfrenta numerosos desafíos. Uno de los mayores desafíos es cambiar la mentalidad y los hábitos de trabajo de los empleados. Para que este cambio tenga éxito, es necesaria la participación activa de todos los departamentos de la organización.
Otro aspecto importante es el compromiso del liderazgo. Sin el apoyo de la alta dirección, los esfuerzos por aplicar Lean pueden quedar rápidamente en el olvido. La clave reside en que los líderes se comuniquen regularmente con los empleados y se aseguren de que comprendan los beneficios de aplicar Lean.
Además, la falta de conocimientos y habilidades también es un obstáculo importante. Muchos empleados pueden no estar familiarizados con los nuevos procesos, lo que requiere tiempo para comprenderlos y adaptarse. Para superar este problema, es esencial la capacitación regular y la impartición de cursos Lean a los empleados.
Por último, mantener los estándares Lean establecidos también supone un reto importante. Las empresas necesitan contar con procesos y sistemas claros para supervisar la implementación y el mantenimiento de las mejoras logradas.
Conclusiones clave
- La Manufactura Lean se centra en optimizar los procesos de producción, reducir el desperdicio y crear valor para los clientes.
- Los siete tipos de desperdicio en Lean deben identificarse y eliminarse para optimizar los procesos.
- La mejora continua de los procesos es un principio fundamental que ayuda a las organizaciones a mejorar la productividad y la calidad de los productos.
- El liderazgo desempeña un papel importante en la promoción de una cultura Lean y en el fomento de la participación de los empleados.
- La Manufactura Esbelta (Lean Manufacturing) ha tenido éxito en diversas industrias, aportando importantes beneficios a las empresas.
En conclusión, la Manufactura Esbelta (Lean Manufacturing) no es solo un método de producción, sino una filosofía que ayuda a las empresas a desarrollarse de forma sostenible. Los resultados que obtienen las empresas al aplicar Lean demuestran su eficacia para optimizar los procesos de producción, mejorar la calidad del producto y ahorrar costes. Para lograr estos beneficios, las empresas deben comprender a fondo la necesidad de Lean e implementarlo de forma sincronizada y bien planificada durante el proceso. La implementación exitosa de la Manufactura Esbelta será la dirección correcta en la era de la producción moderna.